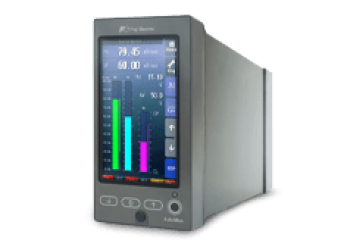
Régulateur multifonction – Série PSC100 – 2 boucles
ref : PSC100À partir de
2928,00 € Demander un devisLa question de la performance énergétique des industries métallurgiques, sidérurgiques et des fonderies est cruciale si le secteur veut réussir sa transition énergétique. Plusieurs instruments de mesure et d’analyse (analyse de gaz, mesure de pression, mesure de débit, mesure de température, mesure de niveau) adéquats peuvent être mis en place pour réaliser des économies d’énergie, réduire sa facture et son empreinte carbone. Économiser et optimiser les consommations énergétiques de chaque procédé est à la portée de chaque industriel.
Les instruments de mesure Fuji Electric accompagnent les entreprises de métallurgie durant chaque phase de leur procédé de fabrication afin de :
Contrôle de la qualité des métaux
Conformité aux normes en vigueur
Efficacité énergétique
Sécurité du personnel et des installation
Dans le four de frittage, les poudres de matières premières (minerais, calcaire et eau) sont soumises à la chaleur pour obtenir une pièce compacte.
Les pièces passent à l’intérieur du four par différentes températures, puis elles sont refroidies et enfin calibrées pour obtenir la forme souhaitée.
Dans ce processus, il est nécessaire de maîtriser la température à l’intérieur du four, de contrôler le rapport air carburant et les émissions nocives.
Le four à coke permet de transformer le charbon en coke par un procédé de distillation à sec.
Le coke est un combustible obtenu par pyrolyse de la houille (à 1100°C) dans un four à coke, à l’abri de l’air, durant plusieurs heures.
Pour optimiser ce procédé, le contrôle de la combustion et la surveillance des gaz d’échappement sont essentiels.
La tour d’extinction, (ou système de refroidissement à sec du coke CDQ), permet de refroidir le coke incandescent à une température appropriée pour le transport. C’est un système de récupération énergétique. Durant le processus d’aspersion d’eau, la chaleur émise par le coke incandescent est récupérée et utilisée pour la production d’électricité ou de vapeur.
Il est nécessaire de surveiller les gaz, CO et H2, afin d’éviter l’explosion lors du trempage.
Le haut fourneau transforme le minerai de fer aggloméré en fonte liquide. Le minerai de fer et le coke sont enfournés par le haut. L’air chaud (1250°C), insufflé à la base du haut fourneau, réagit avec le coke et le charbon pulvérisé et forme un gaz de réduction qui absorbe l’oxygène du minerai de fer. En même temps, de la chaleur est créée qui est nécessaire pour la fusion des minerais réduits. Durant ce processus, de larges quantités de gaz sont générées (CO et CO2).
Pour obtenir le meilleur rendement du haut fourneau, il faut un contrôle de la qualité de la fonte, un contrôle de la combustion du four et une surveillance des émissions de gaz.
La fonte est déversée dans le convertisseur, dans lequel se trouvent des ferrailles. De l’oxygène pur est soufflé sur le bain métallique pour brûler l’excédent de carbone et les impuretés. On obtient de l’acier liquide dit « sauvage ». Il n’est pas nécessaire de produire de la chaleur supplémentaire, car la chaleur générée lors de l’oxydation est soufflée dans le convertisseur. Les gaz de combustion produits dans le convertisseur sont réutilisés pour la production d’électricité ou pour le chauffage dans le processus de laminage.
Pour obtenir une transformation optimale de la fonte en acier liquide, il est nécessaire de surveiller le processus de décarburation et la quantité d’oxygène soufflée.
Les dégazeurs sous vide sont installés dans de nombreux hauts fourneaux et aciéries afin d’améliorer la pureté de l’acier. Le dégazage est un procédé métallurgique qui consiste à ajouter une quantité d’aluminium, avant l’acier, puis d’injecter de l’argon sur l’acier fondu, pour réduire la teneur en H2, 02 et N2, et éliminer certaines inclusions non métalliques.
L’acier fondu décarburé dans le convertisseur est injecté dans une poche de coulée et transporté vers un équipement de coulée continue pour être moulé (en brame, billette ou bloom).
Le gaz argon est versé dans la poche de coulée pour empêcher l’oxydation de l’acier fondu.
La surveillance de l’oxygène est nécessaire pour s’assurer qu’il n’y a pas d’oxygène à l’intérieur de la poche de coulée.
Les brames d’acier sont chauffés dans le four de réchauffe (800°C à 1000°C) de façon à ce qu’elles deviennent suffisamment molles pour le laminage.
Un contrôle de la combustion est nécessaire pour porter le métal à une température permettant sa transformation dans des conditions optimales de qualité, de productivité, d’efficience énergétique, tout en réduisant les émissions polluantes.
La brame est réchauffé dans un four à 1200°C pour rendre le métal plus malléable. Elle est ensuite amincie et étirée par écrasements progressifs entre les cylindres du laminoir. La bande d’acier se transforme en bobines ou en plaques de 1,2 à 20 millimètres d’épaisseur. Les bobines subissent ensuite une deuxième réduction à froid afin d’obtenir un produit aussi fin qu’une feuille de papier (jusqu’à 0,1 millimètre d’épaisseur).
Durant ces procédés, les composants gazeux liés au potentiel carbonique (CO2, CO, CH4, NH3, H2 ou O2) doivent être surveillés et contrôlés.
Découvrez comment les analyseurs de gaz aident à réduire les polluants et favorisent le développement des énergies propres pour un environnement durable.
09 juin 2024