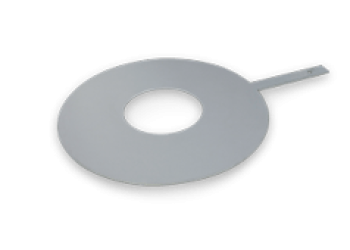
Steam metering is the measurement of steam in industrial processes. This instrument guarantees efficiency, energy savings and cost reduction. Technologies such as depressurizers with pressure transmitter differential, vortex flowmeters and ultrasonic flowmeters are used to obtain accurate measurements. Steam flow measurement is essential in power plants, refineries and the manufacturing industry to optimize operations and avoid energy waste.
Have you ever wondered just how vital accurate steam flow measurement is for numerous industries?
Exact steam flow measurement is essential for ensuring optimal performance, energy saving, and precision in many industries, relying on steam as a primary process component.
Steam flow measurement offers a wide range of technologies used in steam flowmeters, with nuances differentiating each type.
Accurate steam flow measurement is essential for many industries such as power plants, nuclear power stations, chemical plants, refineries and manufacturing units.
With steam being a key player in energy transfer and process operations, precise measurements can lead to better energy saving and optimal system performance.
Inaccurate measurements, on the other hand, can lead to energy wastage, increased costs, and process inefficiencies.
Steam flow meters come in various technologies, each with its own advantages and specific applications. DP steam flow meters, vortex flow meters, turbine flow meters and ultrasonic steam flow meters are among the most popular for steam flow measurements.
Differential pressure flow meters rely on a pressure difference (often using orifice plates) to determine flow velocity, and subsequently, the volumetric flow.
On the flip side, vortex flow meters measuring principle is using a bluff body to generate vortices at a frequency that corresponds to the flow velocity. This approach yields a measurement of the volumetric flow rate.
Similarly, ultrasonic steam flow meters are adept at gauging steam flow. They accomplish this by utilizing sound waves to ascertain the time difference between transmitted and received ultra-high-frequency signals. To enhance their effectiveness, these flow meters commonly incorporate built-in sensors to compensate for variations in temperature and pressure.
Turbine-based flow meters function on principles akin to vortex flow meters. However, they employ mechanical turbines instead of bluff bodies.
Several factors influence the selection of a steam flow meter.
Process conditions like pressure and temperature, the state of the steam (saturated steam or superheated steam or condensate), straight lengths and installation costs are just a few considerations.
Additionally, the desired accuracy, presence of moving parts, and the need for impulse lines or additional components can all play a role in choosing the right meter for process applications.
Mass flow and volumetric flow are two essential parameters in steam flow metering.
Mass flow refers to the mass of steam passing through a system per unit time, and is essential for processes where the quantity of material (in this case, steam) is important.
Volumetric flow rate, on the other hand, concerns the volume of steam passing through a system in a given time. While volumetric flow is directly measured by many meters, to calculate mass flow, additional measurements like temperature and pressure, as well as a flow computer, are often needed due to steam's changing density under various conditions.
Differential pressure flowmeters are a mainstay of steam flow measurement. By creating a pressure difference using components such as an orifice plate, venturi tube or nozzle, a V-Cone flow meter, Pitot tube and differentia pressure transmitter , this category of steam meter determines the flow velocity and then calculates the flow velocity . The linear relationship between pressure difference and flow rate makes these devices reliable and widely used. However, they do require impulse lines and can have some energy loss due to the presence of the orifice plate.
The design simplicity, combined with the lack of moving parts, makes them a reliable choice for many applications, ensuring longevity and consistent performance over time.
Vortex flowmeters operate on the principle of a vortex created by an unshaped body placed in the flow stream, generating alternating vortices downstream. The frequency of these vortices is directly proportional to the flow velocity of the steam.
This makes vortex flowmeters efficient in measuring the flow velocity with good accuracy. One of the distinctive characteristics of vortex meters is their ability to handle a wide range of flow rates, from low to high, without compromising on measurement accuracy.
Ultrasonic flowmeters for steam utilize sound waves to measure the velocity of saturated steam flows within a pipe, subsequently determining the volumetric flow rate.
With their innovative technology, these meters offer several advantages over traditional metering methods.
Firstly, they are non-invasive, meaning they can be clamped onto the outside of pipes without the need for any intrusive installations or process interruptions.
Secondly, with no moving parts, these meters are not only low-maintenance but also suffer from less wear and tear over time. Moreover, their ability to measure saturated steam conditions and their high accuracy in various flow conditions make them versatile for a range of applications. The absence of obstructions within the pipe steam lines ensures minimal pressure drop, further promoting energy saving in many industries.
In the world of steam flow metering, there are many subtleties: from the different measurement techniques to the nuanced decisions behind the choice of a specific steam flow meter, a fundamental understanding of this critical area is paramount.
Remember, precise steam flow measurement is more than just numbers; it's about enhancing efficiency, achieving energy saving, optimizing performance, and ultimately reducing cost in countless industries.
Different applications may require different types of flowmeters. However,differential pressure flowmeters and vortex flow meters are among the most commonly used for steam applications and other fluids like liquids and gases. With that said, the emergence ultrasonic steam flowmeters and the advantages they bring to the table make them a compelling choice for many modern applications, bridging the gap between tradition and innovation.
Absolutely! Clamp-on ultrasonic flowmeters are a groundbreaking innovation in steam flow metering. They can be used in steam applications, offering a non-intrusive and efficient method of measurement. Fuji Electric steam flowmeters are suitable for saturated steam measurement including volume and mass flow at temperatures up to 180°C. By harnessing the power of ultrasonic waves and advanced sensor technology, these flow meters provide accurate measurements without the need to penetrate or modify the piping system. This not only simplifies the installation process but also minimizes potential maintenance concerns reducing the total cost-of-ownership. The innovation behind this technology is truly remarkable, making it an increasingly popular choice for industries seeking precision combined with ease of use.
Steam flow rate can be calculated using the measured flow velocity and cross-sectional area of the pipe. Additional parameters like temperature and pressure might be needed for mass flow calculations.
The flow rate of steam can vary based on the system and application. It's best to refer to specific system data or measurement devices for accurate values. Using a steam flowmeter is the most reliable method of accurately determining steam flow. This device accurately measures speed, pressure and temperature to calculate steam flow.