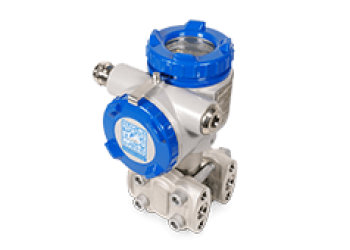
The differential pressure transmitter or deltaP transmitter is a device that measures the pressure difference between two points in a system. This type of industrial pressure transmitter can measure very low differential pressures with great precision. A key element in fluid mechanics, the differential pressure sensor is used to regulate and control industrial processes. They can also be used to measure tank levels, or to monitor the flow of liquid or gaseous fluids.
It also detects gas or liquid leaks, identifiesfilter clogging, and helps monitor the performance of motors, pumps and hydraulic systems.
Download the brochure and find out how to improve your measurement accuracy with Fuji Electric differential pressure transmitters .
The pressure transmitter high-precision FKC differential models from pressure transmitter Fuji Electric measure differential pressure and transmit an electrical signal in the form of a 4-20 mA analog output.
Designed and manufactured in France, these differential transmitters feature a patented, reliable and resistant silicon capacitive chip, combined with advanced digital signal processing. This combination guarantees exceptional performance in terms of accuracy and stability.
Features such as digital signal processing and flexible mounting options enhance the overall efficiency of the measurement system.
This type of industrial pressure transmitter is particularly well suited to applications requiring very high accuracy, even at very low differential pressures.
ROBUST DESIGN
LOW DIFFERENTIAL PRESSURE
EXTREME TEMPERATURES
Pressure transmitter differential with diaphragm seals
Differential diaphragm level sensor
Pressure transmitter for level or density measurement with diaphragm seal PFA
Differential pressure is a fundamental concept in industrial process control.
It refers to the pressure difference between two points in a system.
This measurement is essential for many applications, including flow measurement, level measurement and filter monitoring.
Differential pressure transmitters are specialized measuring instruments, designed to accurately measure this difference and provide a reliable signal, essential forautomation and process control. By monitoring differential pressure, industries can optimize the performance of their production equipment, guarantee efficient operation and maintain the safety and reliability of their installations.
Whether controlling fluid flow, monitoring filter condition or regulating tank levels, differential pressure measurement is a key lever for achieving high levels of performance and efficiency in many industrial sectors.
Differential pressure (dp) is the difference in pressure between two points.
The differential pressure cell compares two pressures measured between two points:
In this way, the differential pressure sensor converts the pressure difference (HP-BP) into a 4-20mA analog signal.
Differential pressure transmitters are available in a range of types, each designed to meet specific measurement requirements and a variety of operating environments.
Traditionally mounted transmitters are commonly used for general-purpose applications. On the other hand, diaphragm seal transmitters with an offset diaphragm are ideal for processes involving aggressive or contaminated fluids, as the diaphragm system isolates the sensor from direct contact with the process fluid.
Digital differential pressure transmitters offer enhanced accuracy and advanced features, making them particularly suitable for applications requiring precise control and data integration in automation systems.
The choice of transmitter depends on several factors: nature of the fluid, desired measurement range, environmental conditions, installation constraints or maintenance requirements.
Differential transmitters with electronic display provide a simple, effective solution for direct visual reading of a pressure difference on a single dial. They are widely used in systems requiring fast, reliable local control.
Choosing the right type of differential transmitter ensures accurate measurement and reliable performance in a wide range of industrial applications.
The differential pressure sensor has two pressure measurement ports: one for low pressure (BP or LP) and one for high pressure (HP).
Each port is connected to a metal membrane made of stainless steel or another material.
When the differential pressure of the industrial process is applied across each of these ports, it deforms the two membranes.
The pressure transmitter capacitive system measures pressure differences by deforming two metal diaphragms.
The metal diaphragms will transmit the measured differential pressure via an internal transmission fluid (oil) to the micro-capacitive electronic chip.
The differential pressure exerted on either side of this element will compress and deform the chip.
The deformation measured is proportional to the differential pressure to be measured.
The signal is then processed digitally by the electronics unit to convert the deformation into an analog 4-20 mA and digital HART signal.
A differential pressure transmitter can display positive or negative values, depending on the direction of the measured pressure. When the pressure on the low side becomes higher than that on the high side, the transmitter indicates a negative value, thus clearly identifying the direction of the pressure difference in the system.
Flow measurement is one of the most widespread applications for differential pressure transmitters in industry.
The principle involves creating a pressure drop across a primary element or depressurizer - such as an orifice plate, Venturi tube or Pitot tube - installed in the pipe. As the fluid flows through this restriction, the transmitter measures the pressure difference between upstream and downstream of the primary element.
This pressure difference is directly proportional to the flow rate, enabling precise monitoring and control of process flows.
Pitot tubes are particularly well-suited to measuring flow at a localized point in the pipe, making them useful for applications requiring point-in-time analysis of fluid velocity.
The use of differential pressure transmitters for flow measurement is a reliable and proven method that contributes toprocess optimization, quality control and the efficient operation of production systems.
Differential pressure transmitters are also widely used for level measurement in tanks and reservoirs.
In this type of application, the transmitter detects the pressure difference between the bottom and top of the tank, a value directly correlated to the liquid level inside. This method is suitable for both open and closed tanks, providing a flexible solution for a wide range of process requirements.
The use of diaphragm seals is particularly recommended for corrosive, viscous or contaminated liquids, as they protect the transmitter while guaranteeing long-lasting measurement accuracy.
By integrating differential pressure transmitters with other process instruments - such as sensors or flowmeters - operators obtain a coherent, global view of their plant, improving process control and equipment protection, even in the most demanding environments.
The various types of differential pressure transmitters are used in a wide range of industrial applications. These include flow measurement, level measurement, filter clogging measurement and density measurement. They are also used for interface measurement.
These differential pressure probes are widely used in many fields. These include thermal energy, thechemical industry, and theoil and gas industry.
Depending on the application, the 4-20 mA output signal can be programmed either as a linear output (output signal proportional to differential pressure) or as a square-root output (output signal proportional to volume flow).
The square-root output function of a differential pressure transmitter measures the flow velocity of a fluid. This method is commonly used in differential pressure flow measurement systems to determine flow rates in industrial installations.
This principle is based on the relationship between fluid velocity and the differential pressure generated by fluid flow(Bernoulli's law),
This relationship is expressed by the following equation:
V = sqrt((P1 - P2) / (1/2 * rho))
P1 = Pressure on the high pressure side -HP) measured upstream of the fluid flow
P2 = Pressure on the low pressure side (LP) measured downstream of the fluid flow
rho = Density of the fluid
V = Fluid velocity
A wide range of measurement ranges and pressure transmitters differential references are available. The selection of measurement ranges goes from 0 to 1 mbar for the lowest scales to 0 to 30 bar for the highest scales.
These differential pressure ranges meet the requirements of a wide range ofindustrial applications, ensuring effective monitoring of fluids (liquids, gases, steam) in your industrial processes.
The wide range of differential pressure transmitters available reflects the diversity of market needs.
Differential pressure sensors have many advantages for industrial processes.
Measuring the pressure difference between two points in a system is simplified by the use of a differential pressure transmitter. This measuring instrument is designed to accurately measure the differential pressure and provide a corresponding digital pressure signal. With a differential pressure transmitter, you can accurately measure the pressure difference without the need for manual calculations.
Another way of measuring differential pressure is to use two transmitters from gauge pressure. You must then measure the pressure separately and manually calculate the pressure difference. This process can be laborious and error-prone.
In addition, if you are using two gauge pressure transmitters transmitters, it is essential to ensure that each transmitter is accurately calibrated for precise pressure measurements. Indeed, if one of the pressure transmitters transmitters is out of phase, the differential pressure measurement may be incorrect.
The use of a pressure transmitter differential pressure gauge eliminates these problems and the risk of measurement errors. You use a single type of device, specifically designed for this application of differential pressure measurement. You get accurate, reliable measurement you can rely on. The commissioning stage of pressure transmitters is simplified by our user guides.
The unit of measurement for differential pressure is the pascal (Pa).
Other commonly used differential pressure units include bar, millibar and mmCE.