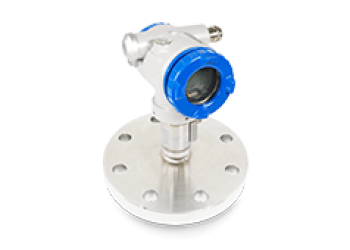
For specific needs not covered by conventional equipment, we design customized sensors at diaphragm seal that can withstand extreme conditions in sectors such as chemicals, oil & gas, paper and food & beverage.
Download the brochure and find out how to improve your measurement accuracy with Fuji Electric diaphragm seals pressure transmitters .
High-tech industries such as chemicals, oil & gas, pulp and paper, food and beverage put their measuring devices to the test.
Critical process media require pressure instrument with high accuracy and reliability.
The reduction of manufacturing costs requires avoiding rejects and production stoppages.
The obsolescence of some measuring devices requires finding replacement instruments that can fit in place.
When your need is specific and no conventional equipment fits the particularities of your installation, we build a custom diaphragm seal transmitter.
Diaphragm seals are used with differential, gauge or absolute pressure transmitters applications.
They can be mounted rigidly, directly on the sensor or with a capillary tube that connects the seal to the transmitter.
The pressure transmitter remote seal and the pressure transmitter cell are welded together without any gaskets, and then filled with an oil or liquid suitable for the application
To understand what is diaphragm seal, we need to dig into the pressure transmitters applications. In some chemical or hygienic applications, it is necessary to isolate the measuring instrument from the process medium pressure.
The diaphragm seal serves as a protective interface between the measuring cell and the process medium.
The flexible diaphragm and the wetted parts are made of a material resistant to the process medium and welded to the base of the measuring cell.
A capillary tube or a connecting sleeve provides the connection between the seal membrane and the pressure sensor measuring cell.
This space must be degassed under vacuum and then filled with a suitable oil filler and sealed.
The measured pressure exerts a force on the outer surface of the membrane.
As the diaphragm flexes inward, it attempts to compress the fill fluid inside the instrument. The pressure is transmitted hydraulically to the pressure gauge.
This fill fluid is designed to resist compression, so the force is channelled directly to the measuring cell.
The entire operation of the diaphragm seal pressure transmitter is based on Pascal's principle.
This principle states that a pressure exerted on a fluid is transmitted without loss through the fluid in all directions.
For this process to work, the displacement force of the diaphragm must be greater than the force required to move the sensing element in the measuring cell.
In practice, this means that the smaller the force required to move the sensing element, the easier it is to build an accurate sealing system.
To ensure the integrity of the manufacturing process, it is necessary to know when to install a seal pressure transducer.
Remote seal type transmitter is used to measure fluids at high temperatures.
The applications of diaphragm seal pressure transducers are multiple: liquid flow measurement, gas flow measurement, steam flow measurement using remote seal differential pressure transmitter and primary element, fluid level measurement in a tank using diaphragm seal level transmitter, fluid density measurement with remote seal type dp transmitter or advanced pressure measurement.
For food, hygienic and pharmaceutical applications, seals are available with hygienic fittings and flush diaphragms to meet sanitary regulations and requirements.
Depending on the constraints of installation and use, several types of diaphragm seal are available meeting most industry standards :
The mounting adapter is dedicated to either adapt the remote seal to a specific process connection or increase the sensibility of the transmitter with special process conditions.
Consult us for specific diaphragm seals.
pressure transmitters at diaphragm seals can be rigid-mounted or direct-mounted if the temperature does not exceed 150°C.
The use of a capillary limits the effects of process temperature on the accuracy of the instrument.
A capillary length of 500 mm reduces the temperature of the instrument to room temperature.
Capillary length should be kept as short as possible, as it influences measurement accuracy and response time.
Capillaries are available from 0.5 m to 15 m with PVC (-10 to +80° C) or stainless steel (-40 to 350° C) protective sheaths.
Two different capillary diameters allow for optimization of accuracy and time response. The inner diameter is 1 mm for standard applications and 2 mm for special applications.
Temperature variations along the length of the capillary can affect instrument accuracy.
Capillary length applies to both low and high pressure sides for balanced systems.
Applies to low side only for rigid assembly and to high side only for remote mount single seal systems with capillary.
A temperature compensation must be done at the factory to guarantee the accuracy.
For applications involving corrosive fluids, diaphragm seals are available in a range of corrosion-resistant materials (stainless steel, Hastelloy C, Monel, Tantalum, Titanium, Zirconium, Nickel, ...).
Please consult us to determine the most suitable material for your application.
The quality of the surface of the membrane and parts in contact with the fluid is very important for hygienic and sanitary applications (cleaning in place).
To prevent the risk of contamination by substances such as product residues or micro-organisms, it is necessary to check the surface finish.
Various average roughness values are available for diaphragm seals membranes: Ra less than 0.4 to 0.8 µm for smooth surfaces, Ra less than 1.6 µm near welds.
The diaphragm is an elastic metallic measuring element. The membrane is welded on the seal and we check that it is properly mounted with a helium leak test.
It must be as large as possible to be as flexible and sensitive as possible. Its thickness varies according to the materials.
For applications with corrosive fluids, the seal is available in wide selection of diaphragm material : stainless steel, Hastelloy C, Monel, Tantalum, Titanium, Zirconium, Nickel and other corrosion resistant materials. can be equipped with multiple coatings (PFA, PVDF, Gold, Hydroseal...) to resist chemical aggression of the measured fluids.
Thickness varies according to material. The membrane is welded to diaphragm seal , and we check for watertightness with a helium test.
TThe fill fluid used must be suitable for the temperature range of the application.
The minimum and maximum temperatures of the measured medium as well as the ambient temperature must be considered.
In addition, the fill medium must be compatible with the medium being measured, especially for media such as oxygen.
For applications in the food industry, food grade filling oils are available to avoid contamination of the measured medium in the event of membrane failure.
Designation of fill fluid | Operating temperature (°C) | Density (25°C) | |
P abs > 1 bar | P abs < 1 bar | ||
Silicone Oil | -40 à 180 | -40 à 120 | 0,95 |
Fluorinated oil | -20 à 200 | -20 à 120 | 1,84 |
Sanitory oil | -10 à 250 | -10 à 120 | 0,94 |
Silicone Oil | 20 à 200 | 1,07 | |
Silicone Oil | 0 à 300 | 20 à 200 | 1,07 |
Silicone Oil | 10 à 350 | 20 à 200 | 1,09 |
The values given are valid for the most common applications.
For special applications, please contact us and indicate the ambient and process temperature, the pressure to be measured, the static pressure and the vacuum values.
Depending on your specific operating conditions, we can use other fill fluids.
Flushing ring is available as an accessories for diaphragm seal flange with a large choice of materials.
The diaphragm seal flushing ring is mounted between the diaphragm seal and the process flange connection.
It is a part in contact with the fluid.
The remote seal flushing ring has a one or two ports that can be used to flush and clean the surface of the diaphragm.
It can also be used as a calibration ring by applying a pressure through the ports.
These values must be added to the accuracy class of the pressure transducer ±0.065% for the differential and gauge pressure range, and 0.2 % for the absolute pressure range.
However, vacuum accuracy cannot be guaranteed beyond 20 Torr (27mbar abs) in standard versions.
This is because most filling fluids contain microscopic quantities of trapped air or gases, which tend to expand significantly as they approach absolute zero pressure.
This expansion affects the instrument's measuring cell.
Process fluid temperature: minimum -90°C, maximum +400°C, depending on the type of fill fluid used, and the membrane material.
The remote seal pressure transmitter consists of a diaphragm seal (with or without capillary) and a pressure measuring cell.
The diaphragm seal capillary tube is filled with a fill fluid at a specific temperature (usually +20 ±2° C) called reference temperature.
A change in the ambient or measured fluid temperature causes a proportional change in the volume of the fill fluid.
Therefore, this has an effect on the internal pressure of the measuring system and adds an error.
To minimize this error, it is necessary to compensate for the volume change caused by temperature.
Small diameter diaphragms can only compensate for a small volume change.
It is therefore recommended to use seals with diaphragms of the largest possible diameter, depending on the process conditions.
When the process temperature is between +150° C and +250° C, a heat sink must be used between the seal and the measuring cell to avoid temperature diffusion.
Above 250° C, diaphragm seal with capillary must be used to protect the instrument from high process temperatures.
This reduces the temperature of the measuring cell to a value close to the ambient temperature.