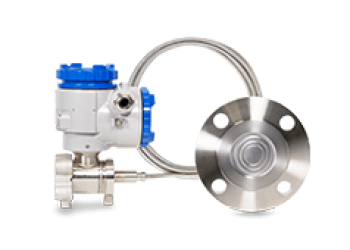
The challenge for paper and cardboard mills is to meet high production requirements while controlling costs and CO2 emissions. To improve theenergy efficiency of industrial paper and board mills, the use ofmeasuring and analysis instruments (pressure transmitter, flowmeter, temperature probe, level sensor, energy meter, analyser gas) is essential. These measuring devices need to be accurate, stable, robust and adapted to your different manufacturing processes to preserve the longevity of your installations and guarantee the quality of your paper and cardboard throughout the manufacturing process.
Fuji Electric measuring instruments accompany paper and board industry professionals during every phase of their paper and board manufacturing process in order to :
Production quality
Energy efficiency
Compliance with standards and regulations
Production optimization
Thepaper industry is a major sector of the world economy, producing essential goods such as paper, cardboard and various by-products. In France, this industry plays an important role, being one of Europe's leading producers of paper and cardboard. It employs thousands of people and generates significant sales. In this article, we'll explore the different stages of paper production, the different types of paper and cardboard, and the environmental and economic challenges facing the paper industry.
Pulp is a mass of fibers made from wood by-products (cotton or linen rags, waste paper, etc.). Wood pulp comes from hardwood and softwood trees. It is made up of cellulose (50%) and lignin and hemicellulose (the remaining 50%). The pulping process takes place in large digesters, where wood chips are mixed with white liquor (such as sodium sulfate or sodium hydroxide), then cooked at very high temperatures and under high pressure. During this process, the cellulose fiber, used as the main material in papermaking thanks to its binding properties, is separated from the lignin and hemicellulose. Some mills use high-quality production processes to guarantee excellent fiber.
Black liquor is used during pulping process. It contains lignin residue, hemicellulose and chemicals. While it is toxic, black liquor can be used as biofuel: the steam obtained after the black liquor went into the recovery boiler serves as fuel for turbo-generator. It can also be used for drying paper or for extracting cooking chemicals.
Recovered papers are mixed with pulp in the pulper. Screening removes large contaminants.
During deinking the addition of chemical separate the hydrophobic particles (inks) from the hydrophilic particles (paper pulp).
The mixture is then aerated in the flotation cell and the froth attached to the hydrophobic particles is collected.
Finally, the pulp is bleached using chemicals.
The pulp slurry (stock + additives) is laid out to form into sheet then drained and dried.
Then the paper may be coated with pigment to increase the strength and pressed with roller to be glossier.
During forming, press and dryer sections, the pulp slurry is drained on mesh wire to form wet fiber web (80% humidity).
The web is squeezed between two press felt (55% humidity) and heated to dry (8% humidity).
During calendering the paper surface is smoothed and coated. Finally it is wound up, cut, packaged and shipped.
Thepaper industry is subject to strictsafety and environmental regulations. Paper mills must comply with rigorous standards to protect workers and surrounding communities. The main safety risks include workplace accidents, fires and explosions. At the same time, mills must also comply with environmental standards to minimize their ecological impact. Major environmental issues include energy consumption, waste management and the reduction of air and water pollution. These measures are essential to guarantee sustainable and responsible production.
The paper industry is a major economic sector, with sales worth several billion euros. In France, the industry is one of Europe's leading paper and board producers, employing thousands of people. The main markets for paper products include printing, packaging and construction. To remain competitive, paper mills must continually invest in research and development, as well as in improving their energy efficiency. These investments are essential to maintain their market position and meet the growing demands of consumers.