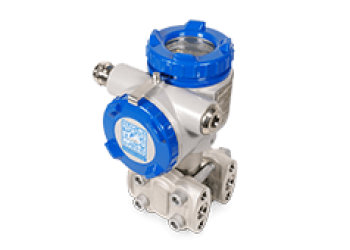
To calculate the accuracy of a pressure transmitter, consider both reference accuracy and on-site performance. The Total Probable Error (TPE) is derived by summing uncertainties like calibrated span accuracy, ambient temperature effects, and static pressure impacts.
In the vast world of process engineering, pressure measurement is the cornerstone of efficient, safe and reliable operations.
As technologies evolve and industries advance, the need for accurate pressure measurement becomes ever more important.
For Maintenance engineers, Instrumentation and Control Engineers, Process engineers navigating the intricacies of pressure transmitters might sometimes feel like threading a needle in a haystack.
But fear not! The essence of achieving optimal performance lies in understanding the subtle nuances that influence a transmitter's accuracy.
This article delves deep into the realm of pressure transmitters, aiming to illuminate the path for maintenance engineers in achieving precise pressure measurements.
We'll start by exploring the importance of defining the accuracy required for specific process applications. Then we'll untangle the difference between on-site performance and reference accuracy, highlighting why this distinction is crucial.
Venturing further, we'll decode the myriad of operating conditions a pressure sensor might encounter, from fluctuating ambient temperatures to varying static pressures, and their consequent effects. Zero shift, span shift, and their cumulative ramifications will also be brought to the forefront.
Finally, the pièce de resistance, we'll furnish you with a comprehensive methodology to calculate the Total Probable Error of a pressure transmitter.
By the end of this article, the hope is that you will be armed with the knowledge and insights to not only select the appropriate pressure transmitter but also to ensure its sustained accuracy throughout its operational lifespan. Let's embark on this enlightening journey together!
The first step is to define the application's required performance for the pressure measurement point.
On-site performance of pressure transmitters should generally be between 0.5 and 2.0% of the calibrated measurement range, depending on the application. The following performance targets are expected, on average, for all service classifications: plant safety and efficiency at 0.5%, environmental control at 1.0%, Scada system and distributed control system at 1.5%, and plant monitoring system and process optimization at 2. 0%. Of course, these are only averages, and some customers will have higher or lower expectations depending on their specific needs. However, these figures give a general idea of the level of performance our customers are looking for.
On-site performance should not be confused with reference accuracy.
There are two distinct concepts when discussing measurement systems :
This is the accuracy of a pressure transmitter sensor under specific, controlled conditions, usually in the laboratory. It provides a standard or reference against which the sensor's performance can be compared. Reference accuracy includes the combined effects of non-linearity, hysteresis and non-repeatability under these defined conditions.
This refers to how a sensor or measurement system performs in real-world conditions or in its actual intended environment.
Several factors can influence on-site performance, including ambient temperature variations, static pressure effect, Stability over time, Influence of supply voltage, Mounting position and other environmental factors.
On-site performance might differ from the reference accuracy due to these external influences.
In practice, while a pressure transmitter might have excellent reference accuracy under controlled conditions, its on-site performance may vary based on the complexities and unpredictabilities of the real-world environment. Therefore, it's crucial to consider both when evaluating or deploying a pressure sensor for a specific application.
The second step is to define the operating conditions to which the device will be exposed.
Depending on the application, pressure transmitters may be subjected to significant variations in ambient temperature.
For example, if a pressure transmitter is used in an outdoor application, the ambient temperature may vary from -20°C to 60°C. This is very different from laboratory use with a stable and air-conditioned ambient temperature.
The other parameter to consider is the static pressure on the process.
In the case of a differential pressure measurement, the higher the static pressure, the more the accuracy will be degraded. For absolute and gauge pressure sensors, the effect of static pressure is zero.
Knowledge of these factors that can influence accuracy enables us to calculate the Total Error Probable (TEP), which defines the accuracy of pressure transmitter under the application's installation conditions, when all individual sources of error are combined. This total performance error is the difference between the most positive and the most negative measurement deviation from the actual pressure. It is calculated by combining all possible errors within the application's operating conditions.
The probable total error value is used to define the worst-case performance of the pressure transmitter installed on site.
Factors such as ambient temperature and static pressure have a certain influence on the accuracy and performance of pressure transmitter. Their influence affects both the zero point and the set measuring range of pressure transmitters, resulting in measurement deviations or inaccuracies.
We have previously determined the desired on-site accuracy for the application, determined the installation parameters that influence the accuracy of our measurement and their influence on zero shift and span shift.
The next step is to calculate the Total Probable Error using the specifications available on the pressure transmitter manufacturer's website (specification sheet). This calculation consists of the sum of the square roots of the uncertainties related to the reference accuracy and the installation factors like the ambient temperature and the static pressure effect.
The Total Probable Error of the device comprises the reference accuracy, the ambient temperature effect, the static pressure effect and is calculated using the following TPE formula:
Probable total error = ± √ ((E1)²+(E2)²+(E3)²)
E1 = Nominal accuracy of calibrated scale or reference accuracy
E2= Effect of ambient temperature
E3 = Effect of static pressure
E1. Nominal or reference accuracy
Nominal accuracy must be calculated on the calibrated or adjusted scale. Reference accuracy includes maximum uncertainty errors for hysteresis, non-linearity and non-repeatability.
E2. Effect of ambient temperature
pressure transmitters are calibrated in the laboratory at a stable ambient temperature. The ambient temperature at the place of application may be different. This temperature has an influence on the electronic components of the measuring instrument, and an inaccurate measurement may result. Manufacturers of pressure transmitters, such as Fuji Electric, generally express this effect in increments of 28°C.
E3. Effect of static pressure
Static pressure errors can be caused by several phenomena inside the pressure transmitter. These include the deformation of metal diaphragms under line pressure, and the balance of filling oil volumes. Suppliers generally define the influence of static pressure every 10 MPa of pressure variation. The effects of static pressure on a differential pressure transmitter can manifest themselves in zero and span shifts. This phenomenon is sometimes referred to as the "static pressure effect" or the "line pressure effect".
Effect on zero :
This is the offset of the sensor output signal when there is no differential pressure in the transmitter, but there is static pressure or line pressure applied.
Tip: the effect on zero can be eliminated by "zero adjustment" under static pressure conditions, which means that the transmitter can be recalibrated or adjusted under static pressure to bring its zero point back to the correct reference level.the transmitter is "informed" that the output current under static pressure, without differential pressure, should represent zero. This effectively compensates for the effects of static pressure on the zero reading.
Effect on scale :
This is the change in transmitter output range due to static pressure or line pressure.
We will consider for our example the following service conditions for our application.
We use the specifications below for the Fuji Electric FKC differential pressure transmitter to calculate overall performance.
datasheet Download datasheet to find out more about pressure transmitter Fuji electric's technical specifications!
So, first, let's consider the right model for the required pressure measurement range and for the application operating conditions following this pressure transmitter selection guide.
The span setting must be set to the nearest of the transmitter cell upper range limit to obtain the best accuracy.
For the pressure measurement of 0-100 mbar, we select the FKC..33 model that offers the closest range of 0/320 mbar.
Models | Static pressure limit MPa {bar} | Measurement ranges kPa {mbar} MIN | Measurement ranges kPa {mbar} MAX | Possible settings kPa {m bar} |
---|---|---|---|---|
FKC 11 | -0.1 to + 3.2 {-1 to + 32} | 0.1 {1} | 1 {10} | ±1 {±10} |
FKC 22 | -0.1 to + 10 {-1 to + 100} | 0.1 {1} | 6 {60} | ±6 {±60} |
FKC 33 | -0.1 to + 16 {-1 to + 160} | 0.32 {3.2} | 32 {320} | ±32 {±320} |
FKC 35 | -0.1 to + 16 {-1 to + 160} | 1.3 {13} | 130 {1300} | ±130 {±1300} |
FKC 36 | -0.1 to + 16 {-1 to + 160} | 5 {50} | 500 {5000} | ±500 {±5000} |
FKC 38 | -0.1 to + 16 {-1 to + 160} | 30 {300} | 3000 {30000} | ±3000 {±30000} |
FKC 43 | -0.1 to + 42 {-1 to + 420} | 0.32 {3.2} | 32 {320} | ±32 {±320} |
FKC 45 | -0.1 to + 42 {-1 to + 420} | 1.3 {13} | 130 {1300} | ±130 {±1300} |
FKC 46 | -0.1 to + 42 {-1 to + 420} | 5 {50} | 500 {5000} | ±500 {±5000} |
FKC 48 | -0.1 to + 30 {-1 to + 300} | 30 {300} | 3000 {30000} | ±3000 {±30000} |
FKC 49 | -0.1 to + 30 {-1 to + 300} | 500 {5000} | 20000 {200000} | {+20000,-10000} {+200000,-100000} |
Accuracy rating of Calibrated Span or reference accuracy
Accuracy: (including linearity, hysteresis & repeatability) |
For models from 32 kPa to 3000 kPa |
EMR > 1/10 of maximum scale: ±0.065% of EMR or ±0.04% of EMR as an option |
EMR < à 1/10 de l’échelle maximale : ± (0.015 + 0.005 × Ech.max/EMR ) % de l’EMR |
The best reference accuracy included maximum uncertainty errors for hysteresis, non-linearity, and non-repeatability is ± 0,04% of span for the Fuji Electric FKC pressure transmitter.
E1 = 0.04 % *100
E1= 0.04 mbar
Ambient Temperature Effect
Influence of temperature |
---|
The values below are given for temperature variations of 28°C between -40°C and +85°C. |
Max. measurement range | Effect on zero (% of TRA) | Total effect (% of TRA) |
---|---|---|
"1"/100 mmCE {10 mbar} "2"/600 mmCE {60 mbar} | ± (0.125+0.1 Ech.max/EMR)% (0.125+0.1 Ech.max/EMR) | ± (0.15+0.1 Ech.max/EMR)% (0.15+0.1 Ech.max/EMR) |
"3"/32kPa {320mbar} "5"/130kPa {1300mbar} "6"/500kPa {5000mbar} "8"/3000 kPa {30000mbar} "9"/20000 kPa {200000mbar} | ±(0.075+0.0125 Ech.max/EMR)% % (0.075+0.0125 Ech.max/EMR) | ±(0.095+0.0125 Ech.max/EMR)% % (0.095+0.0125 Ech.max/EMR) |
In our example, the difference in ambient temperature is 28 °C.
Here we consider the total effect of the temperature effect.
E2 = ± (0.095 + 0.0125*320)%
E2= ± 0.135 mbar
Influence of static pressure
Static pressure | Effect on zero (% of maximum scale) |
---|---|
"1" / 100 mmCE {10 mbar} "2" / 600 mmCE {60 mbar} | ± 0.1% / 0.1 MPa {1 bar} ± 0.063% / 1 MPa {10 bar} |
"3" "4" | ±0.035% / 6.9 MPa {69bar} ±0.035% / 6.9 MPa {69bar} |
We consider here the zero offset of the static pressure effect.
E3 = ± 0.035*320%
E3 = ± 0.112 mbar
We can now calculate the probable total error.
Total Probable Error (TPE)
Probable total error = ± √ ((E1)²+ (E2)²+ (E3)²)
E1= Nominal accuracy of calibrated scale
E2= Effect of ambient temperature per 28°C
E3 = Effect of static pressure per 6.9 MPa
TPE = SQRT ((0.04)^2+(0.135)^2+(0.112)^2)
TPE= 0.179 mbar
TPE= 0.179 % of span
The process application required an accuracy of ± 0.2% of span. The sensor will measure a differential pressure of 100 mbar under normal operating conditions. The required performance of the field-installed sensor will be ±0.5 mbar. We can conclude that the pressure transmitter differential Fuji Electric FKC is suitable for this application. To complete our analysis of pressure performance, we can add a further factor influencing on-site pressure accuracy.
Overrange effect
Overpressure refers to a situation in which the pressure exceeds the maximum calibrated range of the measuring device. Such conditions may arise in the event of an accident or abnormal situation. The accuracy of pressure transmitters is also affected by overpressure. Manufacturers of pressure transmitters, such as Fuji Electric, generally express this effect in terms of maximum working pressure.
Static pressure | Effect on zero (% of maximum scale) |
---|---|
"1" / 100 mmCE {10 mbar} "2" / 600 mmCE {60 mbar} | ± 0.96 % / 3.2 MPa {32 bar} ± 0.31 % / 10 MPa {100 bar} |
"3" "3" "4" "4" | ± 0.10 % / 16 MPa {160 bar} FKC 35, 36, 38 ± 0.15 % / 16 MPa {160 bar} FKC 33 ± 0.26 % / 42 MPa {420 bar} FKC 43, 45, 46 ± 0.06 % / 10 MPa {100 bar} FKC 48, 49 |
E4 = ± 0.15*320%
E4= ± 0.6 mbar
We can now calculate the total accuracy, including the overpressure effect of the range.
Total accuracy = ± √ ((E1)²+(E2)²+(E3)²+(E4)2)
TA = SQRT ((0.04)^2+(0.135)^2+(0.112)^2+(0.6)^2)
TA = 0.62639 mbar
TA = 0.62639 % of span
Pressure measurement remains a foundational aspect of ensuring operational efficiency and safety in the domain of process engineering. Its accuracy is paramount, given the diverse and intricate applications across various industries.
The comprehensive exploration of pressure transmitters in this article underscored the significance of understanding both reference accuracy and on-site performance, as well as the factors that influence these parameters, including ambient temperature effects, static pressure impacts, zero shifts, and span shifts.
Through a systematic elucidation, we've unveiled how to derive the Total Probable Error (TPE) by factoring in various uncertainties such as calibrated span accuracy, ambient temperature influences, and static pressure effects. The given example, using specifications from the Fuji Electric FKC differential pressure transmitter, further simplifies the practical application of this knowledge.
In essence, while selecting a pressure transmitter, it's imperative to ensure that it not only aligns with the required performance parameters but also demonstrates resilience against varying on-site conditions, thereby ensuring its sustained accuracy throughout its operational lifespan. By integrating the insights provided, maintenance and process engineers can undoubtedly make more informed decisions, enhancing both the reliability and efficiency of their systems.
When choosing a pressure transmitter, it's important to opt for a device with minimal impact on the environment.
The advanced floating cell technology of Fuji Electric pressure transmitters provides high immunity against temperature variations, static pressure and overpressure commonly found in the process industry and substantially reduce the overall measurement error.
Fuji Electric's pressure transmitters high-performance class are designed to revolutionize pressure measurement. They are thermally characterized during the manufacturing process to improve reference accuracy and minimize the influence of ambient temperature and static pressure.
This unique thermal characterization process, known as 4D gyration characterized the pressure transmitter cell in the temperature range of -40 to +85 degrees C.
Data are collected during the manufacturing process by recording the zero offset and span at various temperatures using an automated manufacturing process. A non-linear curve-fitting algorithm is performed to characterize unique pressure transmitter behaviour.
Compensation data are permanently loaded into each pressure transmitter cell during this process to actively compensate for thermal environmental effects. The result is a reference accuracy (including hysteresis, non-linearity, and non-repeatability) of less than +0.04% of the full scale over that wide temperature-compensated range.
Eliminate potential errors in measuring differential pressure : Save time and effort by relying on a single device designed specifically for accurate differential pressure measurements